Neoprene rubber, a synthetic elastomer known for its remarkable properties, has become an indispensable material in various industries due to its versatility and durability. Let’s explore the uses of neoprene rubber and the reasons behind its widespread adoption.
1. Automotive Industry
One of the most significant applications of neoprene rubber is in the automotive sector. It is extensively used for gaskets and seals, ensuring dependable airtight and leak-free seals. The outstanding resistance of neoprene to oil, fuel, and heat makes it well suited for the production of hoses and belts used in engines and other automotive systems. Additionally, its ability to absorb and dissipate vibrations is invaluable in reducing noise and vibration in vehicle components, thereby enhancing overall comfort and performance.
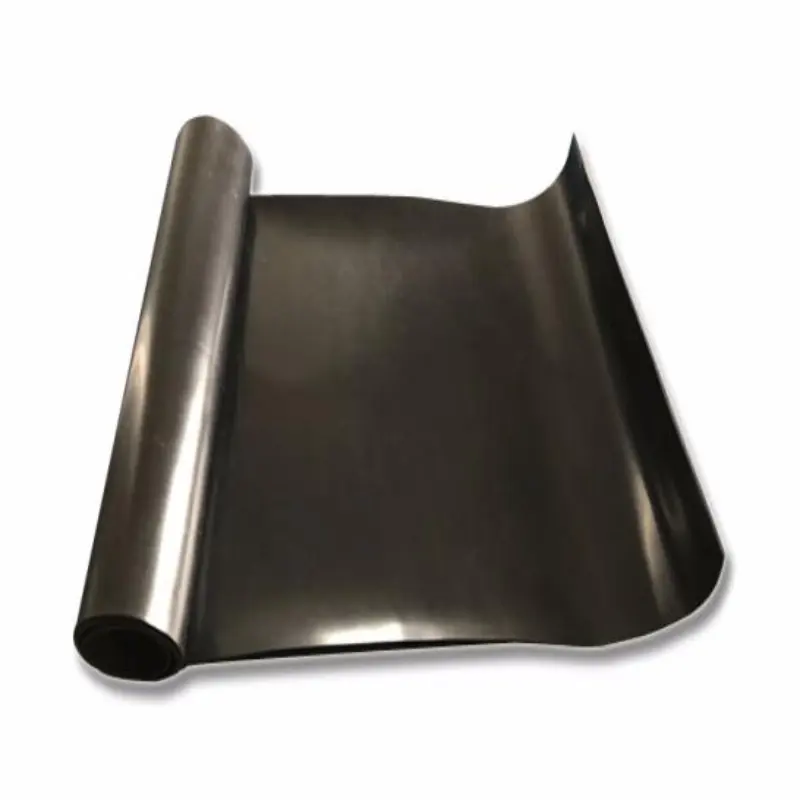
2. Construction Sector
In construction, neoprene rubber is widely used for weatherstripping. Its UV and weather resistance properties make it an ideal solution for providing effective sealing and insulation against outdoor elements. It is also used in expansion joints to accommodate movement and prevent structural damages caused by thermal expansion and contraction.
3. Marine and Aquatic Domain
Neoprene’s water resistance and insulation properties make it the go-to choice for equipment such as wetsuits, gloves, boots, and other protective gear used for watersports and diving. It is also well suited for seals and gaskets found in marine equipment or boats, ensuring reliable performance and preventing water ingress that could potentially cause damages.
4. Electrical Industry
Neoprene rubber exhibits excellent dielectric properties, making it suitable for cable insulation within the electrical industries. It is commonly used to provide insulation and protection against electrical currents or environmental factors. It can also be used in electrical connectors and sealing applications, offering a reliable and moisture-resistant connection.
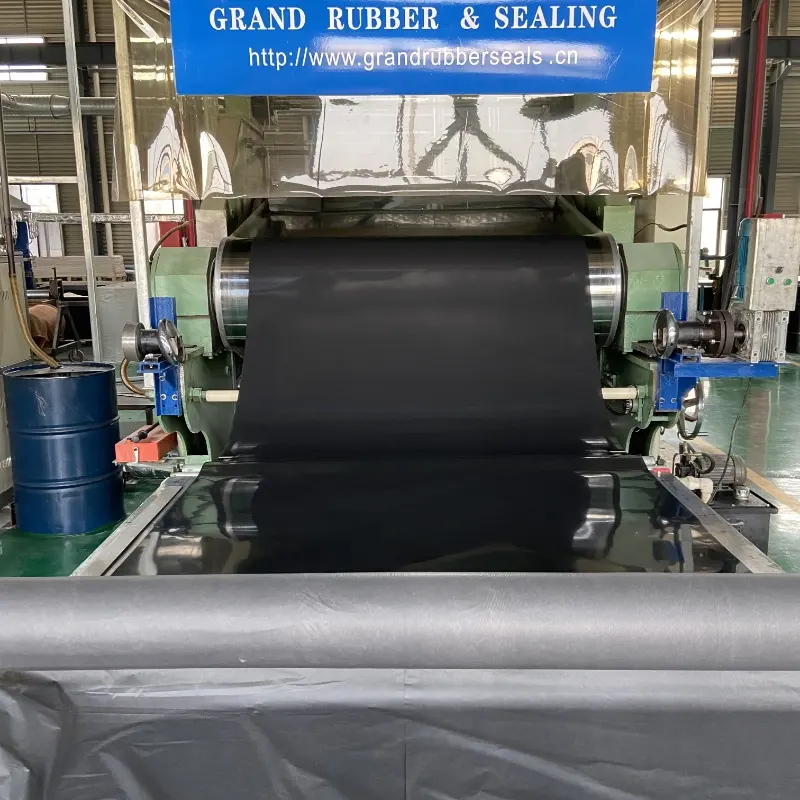
5. Engineering Applications
Within the engineering sector, neoprene rubber serves many purposes. It is particularly valuable for vibration isolation, effectively dampening vibrations to improve the performance and ability of sensitive equipment. Another common use is sealing applications such as O-rings and gaskets, ensuring a secure and leak-proof connection for engineering systems and impact resistance for delicate instruments.
6. Aerospace and Defence
The aerospace and defence sector relies on neoprene rubber for vibration isolation mounts, enhancing performance and accuracy by reducing vibrations in equipment. It can also be used to safeguard delicate aircraft systems and instruments from external forces, where its excellent physical properties and durability can benefit the industry. O-rings and seals are also commonly manufactured from neoprene rubber due to its chemical, oil, and temperature resistance, offering a dependable air-tight seal in diverse aerospace or defence systems.
7. Anti-Vibration and Shock Absorption
Neoprene rubber possesses remarkable anti-vibration and shock absorption properties. It effectively dampens vibrations, minimising noise and enhancing comfort in various applications. Its ability to absorb and disperse impact energy makes it valuable for protecting delicate components and equipment from sudden impacts or vibrations. This property is crucial in industries such as automotive, construction, and machinery, where vibration control and shock absorption are essential for optimal performance and safety.
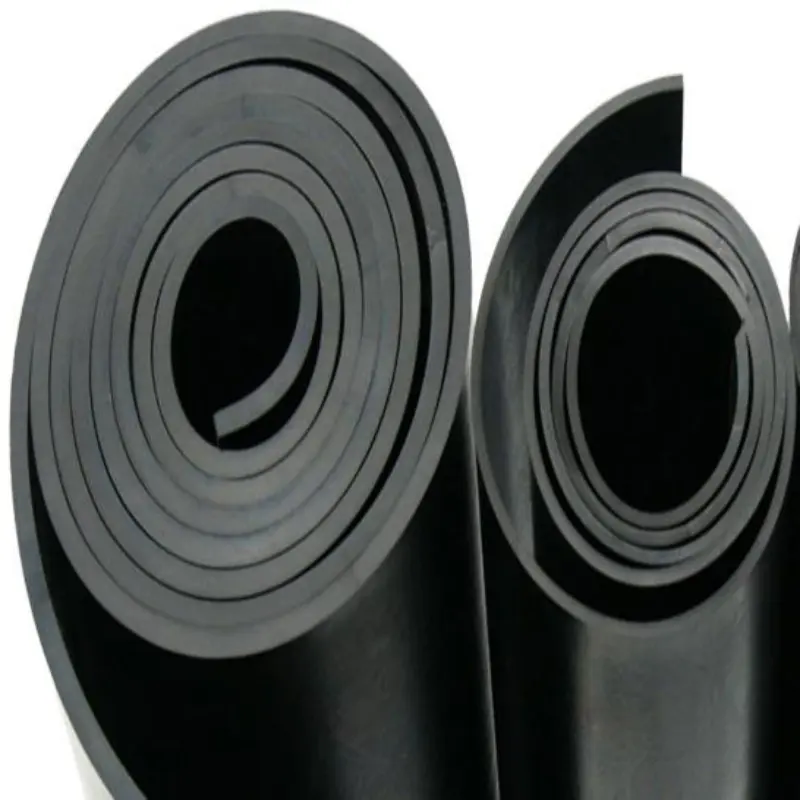
8. Cost-Effectiveness and Other Benefits
Beyond its specific industrial applications, neoprene rubber is also valued for its cost-effectiveness. It offers a balance of properties that make it suitable for a wide range of applications without the high costs associated with some specialty materials. Additionally, its resistance to weathering, UV light, water, chemicals, and ozone makes it a durable choice for long-lasting products.
In conclusion, neoprene rubber’s versatility, durability, and resistance to various environmental factors make it a popular choice across industries. Its ability to meet the demands of different applications, from aquatic gear to aerospace components, showcases its importance in modern manufacturing and engineering.